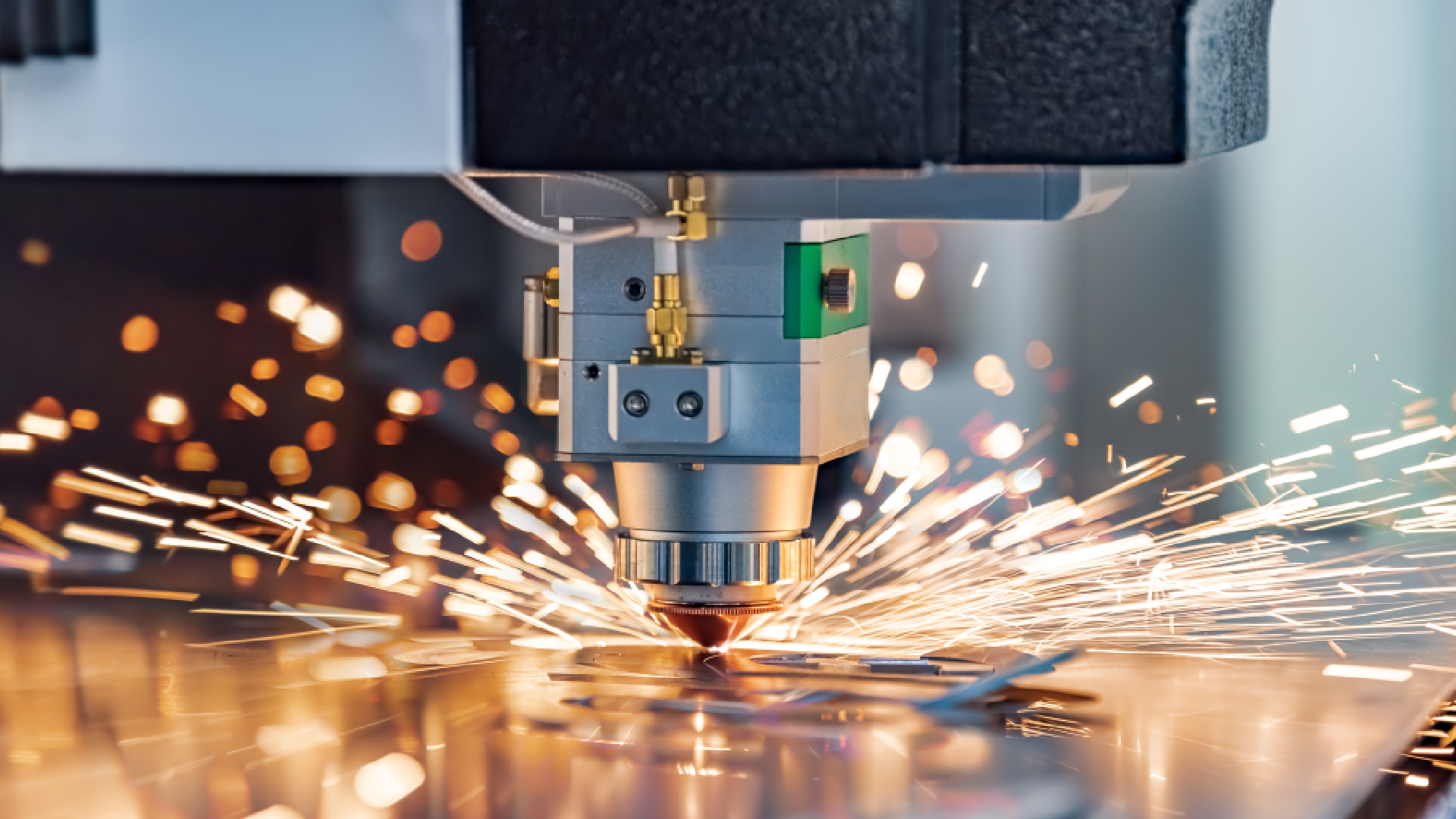
In this guide to the Bill of Materials (BOMs) we will be:
- Defining what a Bill of Materials (BOMs) is
- Explaining how BOMs works in DELMIAWorks & how it gives manufacturers a competitive advantage over other ERP systems
- Outlining the different types of industry specificity that DELMIAWorks offers (particularly plastic manufacturing) & the benefits
Defining what a Bill of Materials (BOMs) is
In the manufacturing sector, the acronym BOM stands for ‘Bill of Materials’, and it refers to the list of raw components, sub-assemblies, intermediate assemblies, sub-components, parts, and the materials (quantities included) that are required to manufacture certain items or end products.
In simpler terms, it can be viewed as a production recipe.
If a manufacturer wants to construct bicycles for example, the BOM would include a list that features individual components such as: the pedal, chain ring and handlebar grip et cetera – all of the parts that are constructed together to make the whole bicycle.
There would also be details on the assembly processes involved to put the bike together – the manufacturing BOMs are usually used alongside Production Routing, which outlines the processes that the production needs to go through in order to manufacture items.
How BOMs works in DELMIAWorks & how it gives manufacturers a competitive advantage over other ERP systems
Both BOMs and Production Routing play a key role in ensuring that both the parts and assembly process work harmoniously to successfully conduct the manufacturing process.
The BOMs and Production Routing systems are typically two separate entities that are used together, however, some ERP systems, such as DELMIAWorks, combine the Bill of Manufacturing and the Production Routing into a single system in order to create a number of manufacturing types and practical advantages for manufacturers.
Because of this, DELMIAWorks has 27 different manufacturing types built-in that offer flexibility over how the BOM is structured. These manufacturing types include:
- Injection moulding
- Material splitting
- Assembly-type production
Outlining the different types of industry specificity that DELMIAWorks offers (particularly plastic manufacturing) & the benefits
The flexibility of having 27 different manufacturing types in DELMIAWorks, makes it possible for the system to fit into a variety of industries.
Take plastic manufacturing for example – if we look at a plastic manufacturing process, DELMIAWorks can factor in things like:
- Cycle time
- Tooling
- Regrind percentage
- Runner & sprue weights
- Cavitation
These open up a whole range of possibilities and benefits for manufacturers that set DELMIAWorks ahead of the competition.
Tooling management for example allows manufacturers to accurately track the use of the tooling they’re using. Manufacturers can also see exactly what materials are required at each stage in the production process.
There are different ways in which manufacturers can backflush material or consume material. There are also placeholders for sprue weights and regrind allowances so that manufacturers can accurately predict the level of scrap that’s going to come out of each cycle.
In terms of material consumption manufacturers can associate a blend as the primary material. So if they are creating a blend of materials, maybe it’s resin with a master batch which is for coloration, then it might be that they need 10% of x to 90% of y. Because we’ve got the ability to create these blends, manufacturers can use aspects like let down ratios.
The system will accurately calculate the amount of material that’s required, the total requirement, but using the blend percentages so you don’t have to do any manual calculations. So the MRP (Material Requirement Planning), even right down to the blend, is accurate.
All of which help to minimise plastic waste, improve overall efficiency and reduce cost.
Where they might have multiple processes, such as for injection moulding, blow moulding or thermo moulding, they can actually have those as subcomponents feeding into the assembly product.
The majority of ERP systems only have one manufacturing type built-in. The functionality to actually properly reflect that process is native to the software, so it doesn’t require any customisation or workarounds. All of the aforementioned functionalities, as well as the reporting and cost attribution comes as standard in DELMIAWorks.
This is in addition to a real time production monitoring engine, so that manufacturers can actually utilise historic overall equipment efficiency (OEE) data to optimise their production schedule.
Get a live demonstration on our upcoming lunch & learn session:
What Makes Bill of Materials in DELMIAWorks so unique for plastics manufacturers?
(Friday 5th May – 12:30pm BST).
Posted by Joe on 2nd May 2023.