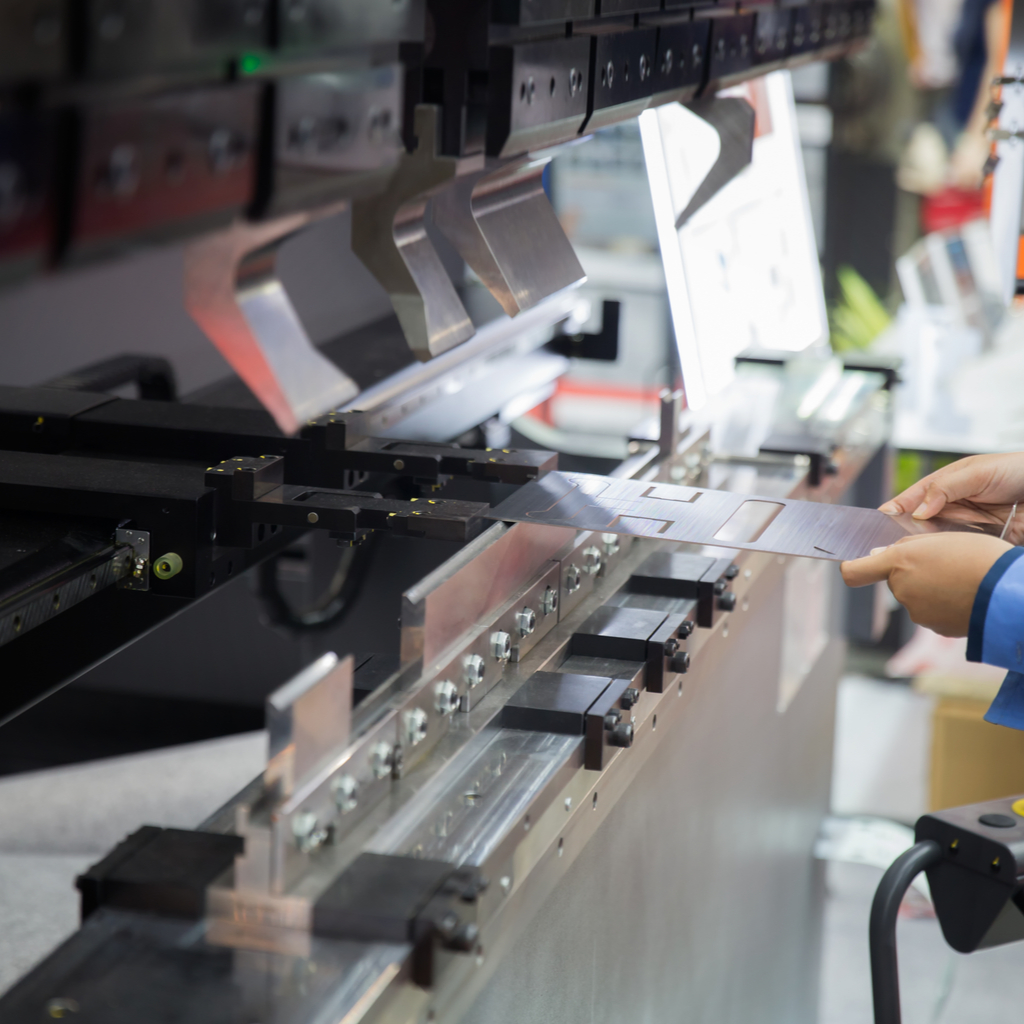
Tom Grigg looks at Bill of Material / Manufacturing (BOMs) in DELMIAWORKS
Learn what a BOM is, and how DELMIAWORKS use BOMs as part of the manufacturing process.
This video for plastics manufacturers is presented by Tom Grigg, Solutions Architect at Proximity. In it, he answers your questions about BOMs:
What does BOM stand for in manufacturing?
In the manufacturing sector, BOM normally stands for Bill of Materials, though BOM may mean different things in different manufacturing ERP systems or organisations – BOM can also stand for Bill of Manufacturing or Bill of Materials.
What is a manufacturing BOM?
A manufacturer’s Bill of Materials, is a list of the raw components or materials that are required to manufacture certain items.
How do manufacturers use BOMs?
Manufacturing BOMs are usually used alongside Production Routing, which specifies the steps that the production needs to go through, in order to manufacture items.
Do you need both BOM and Production Routing software?
Traditionally, BOMs and Production Routing are two separate systems that are used together. Some ERP systems (like DELMIAWORKS) combine the Bill of Manufacturing and the Production Routing into a single system
Transcript:
Hi, I’m Tom Grigg from Proximity Enterprise Solutions.
So, I’m just going to be talking a couple of minutes about BOMs.
Bill of materials, Bill of manufactures, It means different things to different ERP systems, or different organisations.
Traditionally, most BOMs are referred to as a Bill of Materials, which is often a list of components or materials. Raw materials that are required to manufacture certain items.
Alongside the BOMs, you normally get coupled up with production routing, which specifies the steps that a production needs to go through.
Within DELMIAWORKS that’s completely different. The Bill of Materials and the Production Routing are one and the same thing. They’re combined, so you have the actual materials that are required for each step in the manufacturing process. Because of the structure of that, we actually have a number of different manufacturing types.
In fact, we have 27.
Now, these manufacturing types directly change how the BOM is structured – we’ve got manufacturing types for:
- Injection moulding
- Material splitting
- Assembly-type production
And all of a sudden that opens up placeholders for information, such as:
- Regrind percentage
- Runner & sprue weights
- Cycle time
- Cavitation
- Tooling
The manufacturing types can actually allow us to push the BOMs, or the structured BOMs, into particular micro-verticals.
That makes the system extremely powerful, because we can enable it to fit into many different industries, without requiring any customisation, just by restructuring and selecting those different manufacturing types.
Posted by Joe on 3rd June 2020.