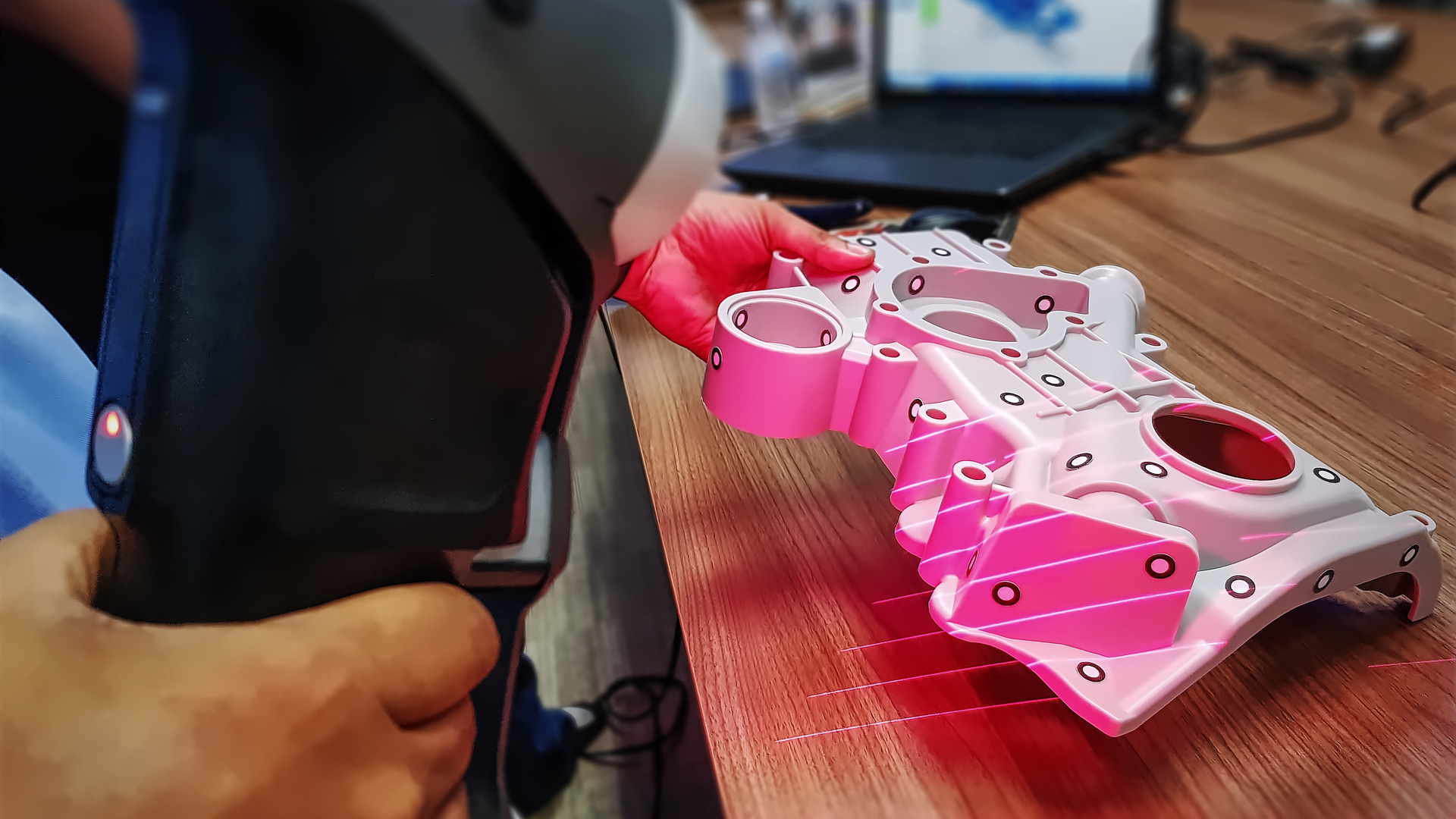
A digital twin is an idea that was first conceived in the 1990’s by Dr Michael Grieves, during his executive management doctorate program at Case Western Reserve University in Cleveland, Ohio.
It was later on, in 2002, when he first introduced the concept as part of his product lifecycle management (PLM) research at the University of Michigan.
Grieves’ vision was that a digital twin could be created to provide a virtual representation of a real-world product or system.
What is a digital twin?
Let’s start with the basics and dig down into what a ‘digital twin’ actually is.
IBM provide a succinct and memorable definition of a digital twin:
““A digital twin (sometimes referred to as a virtual twin) is a virtual representation of an object or system that spans its lifecycle, is updated from real-time data, and uses simulation, machine learning and reasoning to help decision-making.”
In summary, it is the creation of a complex virtual model that is the exact representation of its real-world counterpart.
It provides the ability to collate and represent data from a whole range of systems and turn these into actionable insights.
Whether that be using data to perform simulated stress tests of a physical product, or to provide insights on how a spike in demand might affect the future operations within a product’s lifecycle.
How does a digital twin fit with DELMIA | Works?
In a time where demand for resources and assets across multiple industries has dramatically shifted, as a result of the global pandemic, a digital twin can be used to help manufacturing businesses identify shortfalls or surges ahead of time and adjust their activity to better accommodate these changes.
Creating a virtual representation of the entire product lifecycle, from procurement and planning to tracking and distribution, enables manufacturers to simulate and test the performance of products and processes before doing so in the real-world.
By combining real-time operational insights with cloud-based collaboration, logistical obstacles can be identified and prepared for, waste can be reduced, and greater flexibility developed.
Using a topical example, for manufacturers making vital PPE equipment, a digital twin could be used to both optimise the virtual design of the product and to also enable the manufacturer to model, and simulate, the impact of increased demand on their operations, improve supply chain resilience and predict potential logistical hurdles.
If working with a product, as opposed to a process, manufacturers can make use of a digital twin to reduce new product risk, and provide greater financial visibility, by
validating that a new product design is buildable and will be profitable once produced and sold.
What are the benefits of a digital twin in manufacturing?
If you look at history, we as humans have used diagrams and models to try to understand some of our biggest challenges and to design and create solutions to those problems.
In this digital age however, computers have replaced the pen and paper, 3D modelling has replaced 2D drawings/diagrams and simulation has replaced the need to perform repetitive physical experiments to gather an understanding of a product or system.
So what benefits can a digital twin actually provide for your manufacturing business?
Improved Efficiency and Productivity
Having a digital twin provides a manufacturing business with the ability to virtually test a product by running simulations through ‘what if’ scenarios.
A ‘what if’ scenario is created using a form of logic, by which you would say ‘well when X happens we know that the result is Y, but what happens if we change X to Z? What is the result now?
This is significantly faster than performing a real-world test on a physical product, meaning you could potentially perform thousands of ‘what if’ tests in the time it would take to perform just one physical test.
This can streamline your entire product development roadmap and improve the time-to-market on any of the products produced which are making use of the digital twin.
Reduced Waste
Using sensors on your manufacturing equipment and feeding this information back into DELMIA | Works, and in turn back into the digital twin, means you can look at any areas of the manufacturing process that may be producing large amounts of waste during a cycle.
By using the data you are able collect, you can then analyse, whether or not, there is a better way to operate this particular piece of equipment, or consolidate components to reduce the amount of waste being produced in each cycle.
Increased Quality
Combining a digital twin with a system like DELMIA | Works, which is already capturing real-time information on your manufacturing processes, can allow you to build a culture of continuous improvement.
By constantly taking the data and results gathered and feeding this back into the design and development stages, you can cyclically review and improve the quality and efficiency of your entire manufacturing process.
Improved Business Resilience
Another great benefit of using a digital twin in manufacturing is that it can help your business to become more resilient.
Going back to our earlier example, a company manufacturing vital PPE would have been able to make use of a digital twin during it’s manufacturing process to see what implications a surge in demand, as a result of the pandemic, would have on its logistics process, how production would be affected as the demand grows and where any bottlenecks in the supply chain may be.
Would you benefit from a digital twin in your manufacturing business?
If you think that a digital twin is something your manufacturing business would benefit from, then why not arrange a call with our team here at Proximity to talk about how we can help you work towards a more efficient and effective manufacturing process using digital twins and DELMIA | Works.
Talk to our team today >
Posted by Rob on 12th May 2021.